We are on a mission to limit the amount of hard hats that end up in landfill.
Why hard hats?
Hard hats are mandatory under the Occupational Safety and Health Regulations to ensure a safe working environment and protect workers from falling objects, collision impact and other hazards.
According to the Australian Standards (AS/NZ 1800:1998), hard hats must be replaced every 3 years. These discarded hard hats often end up in landfill, and can take more than 450 years to completely break down.
However there is an opportunity to repurpose these hard hats into valuable resources within a circular economy.
Our Solution.
Through a process of shredding and injection moulding, we repurpose the ABS plastic material from hard hats to produce high-quality shovel handles. This not only helps to reduce plastic waste but also supports a sustainable and circular economy.
We have harnessed a durable building material, renowned for its strength, rigidity and protective qualities and used it to create a handle. This handle excels in function and is designed to optimise efficiency, decrease the risks of injury and offer easy adjustability.
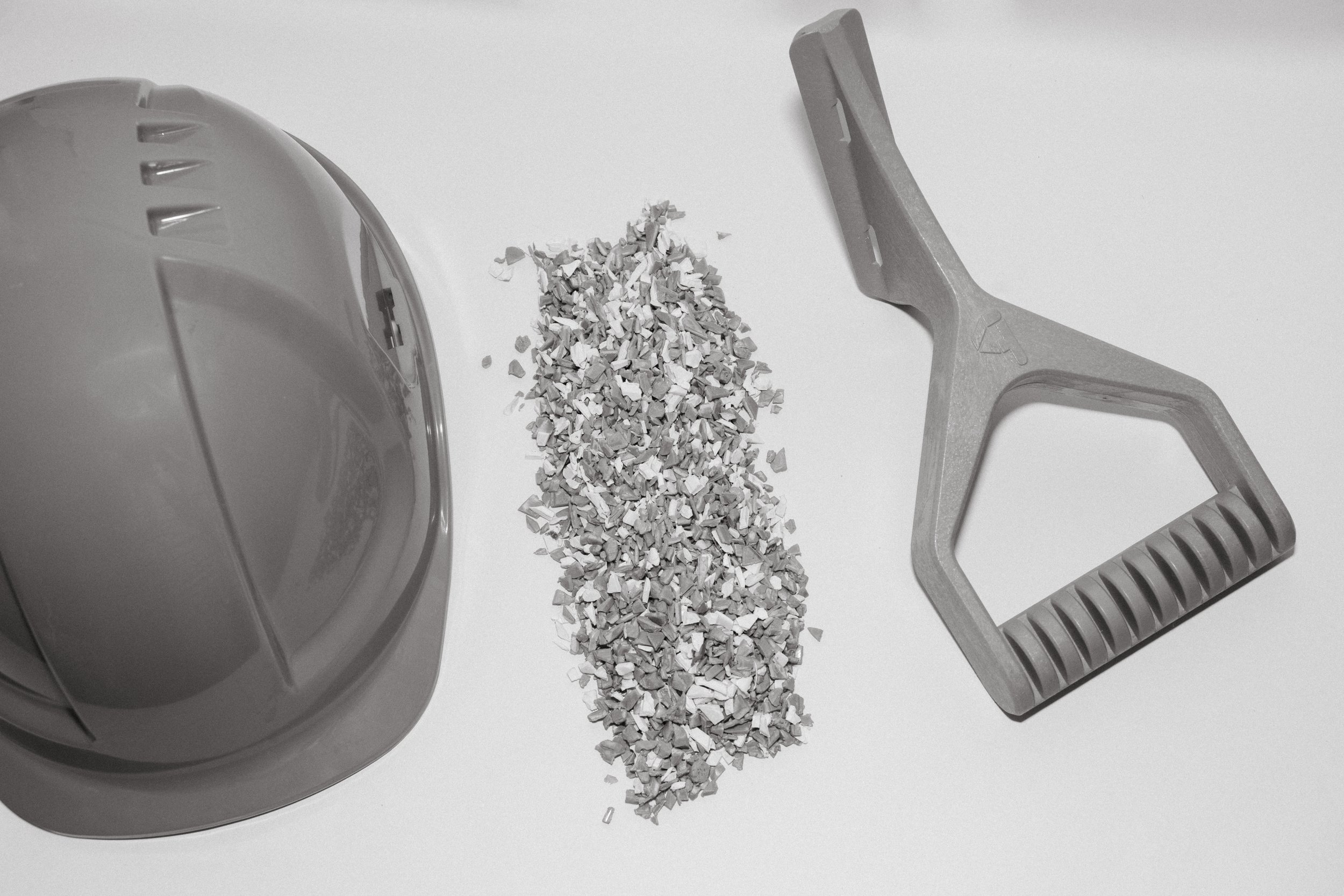
Meet our friends at Defy Design.
Defy are helping us turn hard hats into handles. Below is a step by step process of exactly how this is possible.
-
Defy is Sydney-based company that specialise in designing and manufacturing impactful products made from plastic destined for landfill. They are a passionate team of designers and innovators dedicated to improving the environment through action, rather than words. Defy’s design lead approach to solving complex problems of our past places us at the forefront of closing the loop on our plastic waste streams for good.
The Manufacturing Process.
DISSASSEMBLE
Defy Design separates the hat components, removing items such as the reflective tabs, fastening straps and any stickers.
Note - We are in the process of investigating other potential uses for the straps.
CLEAN
The ABS plastic hard hat shells are washed in a cleaning cycle of any foreign materials and impurities.
MOULD
The material is injection molded into the Back-Up handle. The ABS plastic is heated and liquified through a chamber and coerced into a mould at high pressure. The liquid material fills the shape of the part, it cools, then is ejected out of the mould.
SHRED
The ABS plastic is shredded into a pure, granulated material.